Фасонные железо и сталь
Определение "Фасонные железо и сталь" в словаре Брокгауза и Ефрона
Фасонные железо и сталь Фасонные железо и сталь* — Под этим общим названием в технике и торговле подразумевается металл, оформленный в виде прямых полос с фигурным поперечным сечением, одинаковым по всей длине полосы. В частных случаях полоса может и не быть прямою, а представлять собою форму круга или же, сохраняя прямую форму, иметь по своей длине поперечные сечения различной величины и формы. Во всех этих случаях подразумевается, что длина полосы значительно превосходит наибольший линейный размер ее поперечного сечения. В последнем условии заключается, между прочим, указание и на наивыгоднейший способ воспроизведения таких Ф. металлов. Выковка их в штампах действием молотов хотя принципиально возможна, но крайне затрудняется сложностью профиля и большою длиною полос, обусловливающею необходимость многократных нагревов, а потому большую трату горючего, большой угар металла и мешкотность самой работы, причем все-таки почти невозможно добиться полной идентичности профилей. Отливка таких Ф. полос в литейные формы хотя обеспечивает правильность и идентичность профилей, но встречает почти непреодолимые препятствия в значительной длине требующихся для того литейных форм при сравнительно малом поперечном их сечении. Жидкий металл, текущий узкою струею, застывает, не успев дойти до конца формы; если же и удалось бы предохранить его от застывания, то такая длинная отливка неизбежно покоробилась бы. Ввиду этих неудобств выделка Ф. железа и стали поручается прокатному стану, который производит эту работу быстро и правильно, при минимальном числе нагревов (иногда прямо с одного лишь нагрева), а потому при малом расходе горючего и угаре металла. Поэтому под Ф. железом и сталью подразумеваются всегда изделия (или полуфабрикаты) из железа и стали, полученные прокаткою. Относительного общего устройства прокатных станов см. Вальцы, здесь же разобраны будут лишь принципы и способы, по коим производится в них самая работа прокатки.
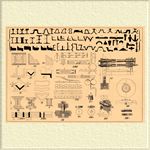 ФАСОННЫЕ ЖЕЛЕЗО и СТАЛЬ.
I. Различные виды профилей Ф. железа и стали: 1—18 — профили рельсов, 19—25 — двутавровых балок, 26—33 — угольников; 34—39 — бандажей, 40 и 41 — швеллеров, 42 и 43 — тавровых балок, 44—65 — разные другие менее употребительные профили. II. Способы пакетирования угольников из полос. III A. Пакет, собранный из угольников. III. Расположение плоскостей сварки: B — при прокатке пакетов, собранных из полос, и C — при прокатке пакетов, собранных из угольников. IV—V. Расположение ручьев для угольников. VI. Выкатка угольника. VII. Приспособление для выправки угольников после выкатки. VIII, IX и X. Способ пакетирования двутавровых балок. XI, XII, XIII и XIV. Последовательный ход обработки болванки проковкою при выделке бандажа. XV. Устройство стана для выкатки бандажей. XVI. Выправка бандажа помощью гидравлического пресса. XVII. Устройство валков стана для выкатки бандажей по способу Мунтона: A — валки чернового стана, B — отделочного.
Ф. катанные железо и сталь изготовляются весьма разнообразных поперечных сечений, представленных на фиг. I. Часть этих профилей вошла в технике, можно сказать, в обыденное употребление, почему они могут быть названы нормальными профилями; остальные профили применяются лишь в узкоспециальных случаях, почему и носят название профилей специальных. Наиболее распространенные из нормальных Ф. профилей суть: Виньолевский рельс, равнобокий угольник, двутавровая балка, швеллер и бандаж (фиг. I, №№ 1, 26, 25, 41 и 34). До конца третьей четверти истекшего столетия прокатные заводы работали исключительно на сварочном железе, поступавшем в стан в виде пакетов (складок), составлявшихся из отдельных полос или прутьев, причем весьма большую трудность представляло добиться полной и совершенной сварки всех отдельных элементов, образовавших пакет. Трудность эта возрастала в еще большей степени в тех случаях, когда приходилось собирать пакет из железа разнородных качеств, как это имело, наприм., место при заготовке пакетов для рельсов. Неодинаковые условия, в которых работают различные части железнодорожного рельса, требовали (при выделке их из железа) крайне сложной пакетировки. Часть пакета, долженствовавшая образовать головку рельса, которая должна быть возможно жестче, чтобы хорошо сопротивляться сильному трению колесных бандажей, выкладывалась из твердого мелкозернистого железа, часть же пакета, соответствовавшая пятке рельса, — из мягкого волокнистого железа, а как эти два сорта железа достигают сварочного жара при различных температурах, то для облегчения их сварки средняя часть пакета и соответствующая стеблю рельса выкладывалась из полос железа переходных степеней твердости. Эта копотливая работа даже при самом тщательном ее выполнении не всегда гарантировала удачность сварки; рельсы расслаивались и трескались. Поэтому, как только открыты были способы получения больших масс железа в жидком виде и возможность получать простою отливкою болванки любых размеров и веса, рельсовое производство тотчас же перешло на литой материал, так что в настоящее время выделка железных рельсов не превышает 1% всей их выработки. Помимо значительного упрощения всех операций, предшествующих прокатке, литой металл, соединяющий в себе с твердостью вязкость, крепость и однородность сложения массы, обеспечивает получение рельсов, вполне отвечающих назначению, и понижает до минимума процент брака. Насколько подходящий материал нашли в нем рельсопрокатные заводы, видно из того, что, например, в России около половины всего болваночного литого железа, а в Западной Европе свыше двух третей — переделываются на рельсы. После рельсов из литого металла стали выкатывать бандажи, балки, угольники, швеллеры и другие ходовые профили, применяемые в строительном и инженерном деле, без дальнейшей механической их обработки или лишь с незначительною обработкою вроде обрезки, сверления или продавливания дыр и т. п. Что касается поделочных профилей, в особенности тех, которые подвергаются горячей обработке, то таковые и до сих пор предпочитается выкатывать из сварочного железа. Главная причина тому кроется в несколько своеобразном отношении литого металла к действию нагрева и механических формоизменений, с которым еще не вполне освоились потребители, привыкшие к сварочному железу. Ввиду этого в России и теперь еще до 2/5 всего катанного железа выделывается из пакетов сварочного железа, а так как в массе его заключается много и Ф. сортов, то, говоря о фабрикации Ф. металла, необходимо иметь в виду как тот, так и другой сырые материалы. При выкатке Ф. профилей необходимо придерживаться следующих общих правил: заканчивать прокатку по возможности с одного нагрева; сообщать пакету поперечное сечение, подобное, в главнейших очертаниях, выкатываемому профилю [Лишь с введением таких Ф. пакетов сделалась возможною выкатка профилей, совершенно невыполнимых при простой призматической форме пакетов. ]; стараться расположить ручьи на валках таким образом, чтобы центр тяжести прокатываемого профиля находился на средней окружности валков, имеющей среднюю же периферическую скорость (этим ослабляется неудобство неравномерного вытягивания, происходящего вследствие того, что частицы металла в одном и том же поперечном сечении полосы движутся с различными скоростями); форму наружных контуров ручьев избирать с таким расчетом, чтобы в тех местах профиля, где частицы металла подвергаются наибольшему вытягиванию, они испытывали наименьшее сдавливание, и наоборот, — и этим предупреждать возникновение в массе металла вредных внутренних напряжений; постепенно уменьшать к концу прокатки степень вытягивания, так чтобы в последних ручьях она была едва заметна; давление, производимое на металл ручьями, не допускать выше того, какое необходимо для плотного заполнения ручьев металлом, иначе излишне сильное давление вызывает в нем трещины; ввиду этого не форсировать давления слишком поспешною сбавкою площадей поперечных сечений ручьев; в быстро идущих станах благодаря возможности закончить прокатку, пока металл еще не остыл и не утратил тягучести, можно, впрочем, сбавлять площади ручьев смелее, нежели в станах, работающих медленно и дозволяющих металлу сильно остыть и затвердеть; прокатку профилей большой высоты следует вести плашмя, т. е. нарезать ручьи так, чтобы наибольший размер профиля имел горизонтальное положение, иначе ручьи слишком глубоко врежутся в тело валка и разница периферических скоростей выйдет слишком велика; не забывать, что чем тоньше какая-либо часть выкатываемой полосы, тем быстрее она охлаждается и ожесточается и тем труднее вытягивается, хотя продолжает еще поддаваться действию сдавливающих усилий; ввиду этого подобные тонкие части следует оформливать окончательно лишь в последних уже ручьях, причем стараться производить это "ребровыми" ручьями (т. е. такими, очертания которых вертикальны или близки к вертикальным); ширину ручьев следует уменьшать по мере удаления от наружной поверхности валка к его оси; при прокатке несимметричных профилей следует рассчитывать ручьи так, чтобы частицы металла внутри профиля подвергались возможно меньшему сдвигу. Помимо изложенных общих соображений, при проектировании ручьев и назначении числа пропусков, заканчивающих всю операцию, необходимо руководствоваться еще и качествами перерабатываемого металла; различием этих качеств объясняется то обстоятельство, что калибровка, дающая вполне удовлетворительные результаты на одном заводе, оказывается иногда непригодною для другого. Прежде чем остановиться окончательно на избранной калибровке ручьев, полезно испытать ее прокаткою пробных полос. Примерами Ф. катанного металла, на которых можно ознакомиться с операциею подготовки сырого металла и самою перекаткою его в изделия, могут служить: для сварочного железа — угольники и тавровые балки, для литой стали — рельсы и бандажи. Угольники выкатываются самых разнообразных профилей, понятие о которых дают №№ с 26 по 33 фиг. I. Наиболее употребительные из них суть прямые угольники с одинаковыми или различной длины сторонами (равнобокие и разнобокие) №№ 26 и 27, применяемые во множестве при постройке мостов, стропил, поворотных кругов, резервуаров и т. п. Они выкатываются размерами от 40 x 40 мм до 160 x 160 мм [Неравнобокие же до 200 мм в длинной стороне.]. При 5—19 мм толщины и весят от 3 до 50 кгр. в погонном метре. Пакеты для них составляются из отсортованных полос сыропроката (мильбарса, см.) с жилковатым сложением, к которым подмешиваются обрезки готовых угольников. Наружные поверхности пакета с двух или со всех четырех сторон перекрываются полосами двусварочного волокнистого железа с целью сообщить металлу большую вязкость и предохранить его от растрескивания при продавливании дыр, обрезке, выгибании и т. д. Мелкие и средние пакеты складываются в форме четырехгранных призм, крупным же сообщается приблизительная форма угольника. На фиг. II, А изображает призматический пакет, составленный из взаимно переплетающихся полос сыропрокатного железа № 2 (сложения смешанного зернистого с жилковатым) и № 3 (сложения жилковатого). Низ и верх пакета перекрыты полосами аа из двусварочного волокнистого железа. Фиг. II, В изображает Ф. пакет, причем заштрихованные полосы изображают двусварочную, волокнистую обкладку, а незаштрихованные — сыропрокат. Иногда пакет собирается прямо из одних угольников (фиг. IIIА); это делается с целью получить более правильные и надежные слои сварки. Если разрезать выкатанный угольник и обработать плоскость разреза кислотой, то следы плоскостей сварки выступают вполне отчетливо. При этом в угольнике, пакет для которого был собран из полос, следы эти располагаются неправильно (фиг. III — В); если же пакет был собран из угольников, то сварные плоскости располагаются правильными рядами (фиг. IIIС.). Прежде чем приступить к составлению пакетов, определяют их вес по весу готового угольника, какой желают из него получить; при этом на угар и обрезки прибавляется от 25 до 30%, а при вычислении по весу пакета его объема прибавляется еще 10—12% на пустоты, остающиеся между отдельными кусками пакета. От 6 до 10 подобных пакетов засаживаются в сварочную печь и в 12-часовую смену делается от 4 до 8 насадок. Для обслуживания одного прокатного стана применяется от 2 до 4 печей. Из печи пакеты относятся к прокатному стану и перекатываются в угольники — мелкие с одного вара, крупные с двух варов. В последнем случае второй вар дается после пропуска через первые же 2—3 ручья, пока болванка еще не очень растянулась и может быть посажена в печь. Общее число пропусков обыкновенно равно 13, из которых первые 8 делаются через грубопрокатное отделение стана, а остальные 5 — через чистовое. Валки имеют обыкновенно диаметр в 0,46 м при длине в 1,12 м. Предпочитаются триo-вальцы, чтобы не передавать полосу через стан. Ручьи нарезаются на валках по большей части так, чтобы линия, делящая угол угольника пополам, была вертикальна, как показано на фиг. IV, но иногда (при мелких неравнобоких профилях) располагают их и так, чтобы одна из наружных сторон угольника (попеременно то длинная, то короткая) была вертикальна (фиг. V). При выкатке самых крупных угловых профилей угол их образуется лишь весьма постепенно, полки же отворачиваются лишь уже в последних ручьях, как это изображено на фиг. VI. Это дает возможность всю предварительную прокатку вести на универсальном стане (т. е. стане без ручьев, в котором различные поперечные сечения образуются соответственным взаимным сближением или удалением двух пар гладких валков — одной с горизонтальными, другой с вертикальными осями). Степень вытягивания при прокатке мелких и средних равнобоких угольников применяется в пределах от 0,2 до 0,5 м за каждый пропуск. Угол профиля последних ручьев должен превосходить действительный угол, требуемый от готового угольника, на 3° — 12°, так как при остывании вышедшего из стана угольника полки его под влиянием действия усадки несколько сворачиваются внутрь, уменьшая образуемый ими угол. Этот припуск сообразуется с величиною конечного угла (угол этот может быть весьма различен), с длиною полок и с темпер. нагрева, при которой готовый угольник оставляет стан. При выпуске из последнего чистового ручья стана угольники предохраняются от сильных прогибов особыми направляющими. Этого, однако же, оказывается недостаточно для получения вполне прямых угольников, а потому они, пока еще не остыли совершенно, правятся услугами специальных приспособлений или механизмов. Простейшее приспособление (фиг. VII) состоит из нескольких опор А, А, А..., расположенных по одной общей горизонтальной линии и снабженных угловыми гнездами с профилем, соответствующим наружному контуру угольника. Над опорами движется по рельсам тележка ВВ, на осях которой закреплены катки СС, оформленные по профилю внутреннего контура угольника и при передвижении тележки вращающиеся. Выправляемый угольник E укладывается на опоры, тележка соответственно нагружается и прогоняется взад и вперед, один или несколько раз, над угольником, который и выпрямляется ее катками. Более сложный механизм, служащий для той же цели, состоит из нескольких пар вращающихся роликов, охватывающих с обеих сторон обе полки угольника и заставляющих последний двигаться между ними. Оси роликов помещены в суппортах, могущих передвигаться и устанавливаться на требуемых взаимных расстояниях. Однако же самая тщательная выправка в горячем состоянии не может вполне предохранить угольник от усадки и коробления при дальнейшем его остывании, поэтому иногда производится дополнительная их выправка уже в холодном состоянии. Обрезка на точную длину производится, пока угольники еще не остыли, при помощи круглых пил. Заработная плата рабочих при выкатке углового железа распределяется средним числом так, что на долю пакетировщиков, грельщиков при сварочных печах и правильщиков приходится по 20%, а на долю вальцовщиков при прокатном стане — остальные 40% этой платы. Двутавровые балки выкатываются также весьма разнообразных профилей, как это видно из №№ 19 по 25 фиг. I. Употребительнейшие из них суть №№ 19 и 25. Балки этого профиля употребляются в больших количествах при постройке зданий, мостов, вагонов и на другие сооружения. Нормальные размеры их: ширина основания от 75 до 75 мм, высота всей балки от 75 до 500 мм, толщина железа от 6 до 20 мм в стержне и от 8 до 25 мм в полках, вес от 13 до 200 кгр. в погонном метре. Были случаи изготовления и более высоких балок. Русские прокатные заводы не катают балок свыше 305 мм высотою и тяжелее 57,5 кгр. в погонном метре. Пакетировка двутавровых балок производится схоже с пакетировкою угольников, т. е. для мелких профилей приготовляются пакеты простого прямоугольного сечения, а для крупных — Ф. сечения, представляющего некоторое подобие будущей балки. Ширина пакета делается всегда значительно более ширины полки готовой балки, а высота его несколько менее высоты балки. Материалами для пакетировки служат сыропрокат и двусварочное волокнистое железо в количестве от 85 до 50% первого и от 15 до 50% второго. Идут в дело также и обрезки готовых балок, угольников и коробчатого железа. Способ размещения этих составных частей в пакете виден на фиг. VIII, представляющей пакет для балки в 160 x 500 мм, причем заштрихованные полосы изображают двусварочное железо, а незаштрихованные — сыропрокат. Обрезки готовых продуктов идут обыкновенно на выкладку стержня пакета (фиг. IX). Иногда пакет окружается со всех сторон двусварочными, полосами (фиг. X). Трудность равномерного нагрева крупных пакетов и, как следствие этого, несовершенство проварки — составляют главную причину ограниченного употребления слишком тяжелых катаных балок, заставляя предпочитать им клепаные. Выкатка балок производится по большей части с двух нагревов. Валки имеют диаметр 0,5 или 0,6 м и располагаются обыкновенно в трех клетках. Число пропусков делается от 8 до 12. Черновой стан снабжается трио-вальцами с тремя ручьями на них; первая клетка отделочного стана — также трио-вальцами и имеет тоже три ручья, чистовая же его клетка имеет лишь два валка (дуо-вальцы) с одним ручьем и служит для сглаживания неправильностей профиля, вызываемых неполным совпадением осей симметрии ручьев, составляющим существенный и трудноустранимый недостаток трио-вальцов. Прокатный стан для ходовых профилей балок требует двигателя силою от 500 до 1000 паровых лошадей. Выкатка балок особо крупных размеров требует и машин более сильных. Так, напр., прокатный стан французского завода Омон (Hautmont), выкатывающий балки в 500 мм высотою, весящие до 200 кгр. в пог. метре, приводится в движение машиною в 3500 сил. Валки этого стана имеют диаметр в 1 м и весят каждый 20 тонн. Балки выкатываются им длиною до 20 м. Стан этот реверсивный (т. е. такой, валкам которого можно сообщать по желанию вращение в ту или другую сторону). Для балок свыше 250 мм высотою предпочтительнее применять реверсивные дуо-вальцы. При калибровке чистового ручья для двутавровых балок необходимо несколько припускать на усадку профили обеих полок; напротив того, ширина части ручья, соответствующей стержню балки, делается чуть-чуть (на 1/3 — 1/4 мм) меньше толщины стержня готовой балки, так как металл в этом месте несколько распухает по выходе из ручья. Все ручьи нарезаются на валках так, чтобы стержень балки занимал горизонтальное положение, а обе ее полки — вертикальное положение. Можно приспособить для выкатки двутавровых балок также и универсальный стан. Тяжелые балки по выходе из чистового ручья подхватываются вращающимися роликами и переносятся ими к круглым пилам, которые обрезают концы балки на должную длину. Неровности на плоскостях разрезов сглаживаются иногда на механических станках с лобовыми фрезами. Кроме сварочного железа, двутавровые балки выкатываются и из литого железа, и литой стали. Рельсы, изготовляемые из сварочного железа, идут для узкоколейных дорог, паровых и конных трамваев и т. п. В огромном большинстве случаев рельсы изготовляются из литой стали, преимущественно бессемеровской. Относительно профиля поперечного сечения рельсов следует заметить, что в этом отношении никакой другой вид Ф. прокатного металла не представляет столь большого разнообразия. Некоторое понятие об этом разнообразии дают №№ 1 по 18, фиг. I. Помимо массивных профилей, как видно из рисунка, существуют еще коробчатые и пустотелые; последние имеют целью сообщать пути эластичность и тем ослаблять удары, испытываемые колесами подвижного состава (подобные пустотелые рельсы выкатываются из труб без шва, полученных в свою очередь прокаткою). — Наибольшим распространением пользуется, однако же, профиль Виньоля (фиг. I, № 1), фабрикация которого единственно и будет здесь описана. Сорт стали, преимущественно употребляющейся на выкатку рельсов, содержит от 0,25 до 0,35% углерода и от 0,30 до 0,90% марганца. Временное сопротивление разрыву такого металла от 55 до 65 кил. на кв. мм при удлинении от 25 до 20%. Сталь отливается в болванки, которые по их нагреве поступают прямо в перекатку; этим устраняется копотливая операция пакетирования. Величина болванок сообразуется с силою прокатного стана, с числом нагревов, за которые предполагается заканчивать прокатку [Так как сталь должна обрабатываться при более низкой температуре, чем железо, и так как она сильнее последнего сопротивляется действию сдавливания, то приходится прибегать при ее обработке к частым повторным нагревам.], и, наконец, с весом выкатываемого рельса, который не должен быть чрезмерен, чтобы не затруднять дальнейшие манипуляции с рельсами. Болванкам придается вид четырехгранных усеченных пирамид со сторонами большого основания от 0,3 до 0,5 м, со сторонами малого основания на 3 до 5 стм меньшими, высотою от 1,5 до 2 м и весом от 1 до 4 тонн. Из одной болванки получаются, смотря по ее весу (в указанных выше пределах), от 3 до 8 рельсов длиною по 9—12 м и весом от 25 до 45 килогр. в погонном метре. Наичаще употребляются болванки на 4 рельса. Болванкам сообщается избыток веса, имея в виду потерю металла на угар и обрезки. Ничто не мешало бы, очевидно, сообщать болванкам фигурное поперечное сечение, подобное избранному профилю рельса, но этого не делают, предпочитая образовать весь профиль прокаткою, чтобы возможно более уплотнить металл и сообщить ему должную однородность сложения. Прежде нагретые болванки предварительно проковывались под 6-тонным молотом двукратно, т. е. с промежуточным нагревом (второй вар), так что, например, болванка сечением в 11x11 дюймов обжималась сначала на 9x9 дюймов, а затем на 7x7 дюймов. После нового нагрева (третий вар) болванка пропускалась через 7 ручьев чернового (болваночного) стана, затем снова нагревалась (четвертый вар) и выкатывалась в 7 ручьях чистового стана в готовый рельс. В настоящее время нагретая болванка поступает прямо в черновой стан, на котором она превращается в квадратного сечения бруски, от 150 до 200 мм в стороне квадрата. Эти бруски разрезаются на соответственное число кусков при помощи секача под паровым молотом, или ножницами, или циркулярною пилою и снова закладываются в печь, а по нагреве (до светло-оранжевого жара) перепускаются через ручьи отделочного стана, который или состоит из двух-трех клеток с трио-вальцами, или же устраивается реверсивным. Малые болванки (на 2—3 рельса) по выходе из грубопрокатного стана не разрезаются на куски и не подвергаются новому нагреву, а передаются прямо в отделочный стан. Число всех пропусков для рельсов делается от 15 до 20. В новейших, могучих прокатных станах с машинами в 2000 до 5000 сил, выкатываются за один вар рельсы четверной, пятерной и даже восьмерной длины. Температура, при которой прокатываются стальные рельсы, имеет огромное влияние на их качества. Она не только должна быть равномерно распределена по всей массе перекатываемой штуки, но, сверх того, быть не слишком высокой в начале прокатки и не слишком низкой в конце ее. Особенно опасно чрезмерное охлаждение к концу операции, так как оно служит причиною возникновения внутренних напряжений, которые делают хрупкою сталь даже вполне доброкачественного химического состава. На многих заводах отлитые болванки предварительно посадки их в печь оставляют свободно остывать и уже затем вновь их нагревают. Это делается ввиду того соображения, что печь сообщает нагрев преимущественно наружным слоям металла болванки, что облегчает прокатку, между тем как не остывшая еще вполне после отливки болванка сосредоточивает сильный жар внутри ее при остывших и даже затвердевших несколько поверхностных слоях, что затрудняет ее прокатку. Также помещают отлитые болванки в теплоуравнительные колодцы Джерса (см. Литая сталь). Выкатанные брусья первопроката или оставляются свободно остывать, или еще горячие сажаются в калильную печь. В первом случае нагрев их длится 4—5 часов, во втором — лишь 2 часа. Каждый нагрев сопровождается угаром металла в количестве от 2 до 4%, что необходимо иметь в виду при дименсионировании болванки. Сыропрокатные бруски предварительно посадки их в печь или направления в отделочный стан обрезаются с концов. Обрезки эти идут снова в переплавку. Потеря металла составляет при этом от 8 до 10%, что также необходимо предусмотреть при задании начального веса болванки. В качестве примера нормальной работы рельсопрокатного стана проследим выкатку двойного рельса, из которого вырезаются два одинарных рельса длиною по 9 м, с площадью поперечного сечения в 40 кв. стм и весом каждый в 342 кгр., т. е. 38 кгр. в погонном метре (что соответствует приблизительно 28-фунтовому рельсу длиною в 30 фут.). Такие двойные рельсы выкатываются за один вар, поэтому горячий угар металла (при нагревании болванки) принимается не свыше 4%; прибавляя сюда 10% на обрезку концов сыропрокатных полос и 5% на обрезку концов готового рельса, полный припуск веса болванки = 0,19 x 2 x 342 = 130 кгр., а полный начальный вес болванки 2 x 342 + 130 = 814 кгр. Удельный вес стали с содержанием углерода 0,25 до 0,35% (какая исключительно и употребляется на выделку рельсов) = 7,85; отсюда, потребный объем болванки — 814/7,85 или 103,7 куб. децим. При среднем сечении болванки в 30 x 30 = 900 кв. стм длина ее, соответствующая искомым объему и весу, = 1,15 м. Размеры же верхнего и нижнего ее сечений можно принять = 278 x 278 и 322 x 322 кв. мм. Коэффициент вытягивания при прокатке в черновом стане принимается средним числом в 1/10, так что после трехкратного пропуска через первый ручей этого стана и двукратных пропусков через последующие 4 его ручья болванка (в общем после 11 пропусков) получает длину 2,7 м и площадь поперечного сечения в 384 кв. стм. Таким образом, коэффициент утонения в болваночном стане получается — 2,34. В приуготовительных валках отделочного стана средний коэффициент удлинения принимается — 0,15, в чистовых же его валках = 0,20; пройдя по одному разу 6 ручьев первого отделения, болванка удлиняется до 6,3 м, а пройдя 7 ручьев второго отделения (также по одному разу), получает длину 19,6 м (следует заметить, что практические коэффициенты удлинения отступают в ту и другую стороны от указанных средних их величин). Из приуготовительного отделения отделочного стана полосы выходят с поперечным сечением в 150 кв. стм, т. е. со степенью утонения в 2,56; готовый рельс, выходящий из последнего чистового ручья, имеет площадь поперечного сечения — 40 кв. стм, т. е. утоняется в этом отделении стана в 3,75 раза. Таким образом, при перекатке на рельс в рассмотренном примере болванка утоняется, в общем, приблизительно в 23 раза. При более сильных станах, допускающих выкатку рельсов трех-четырех-пятикратной и т. д. до восьмикратной длины, разумеется, и утонение выходит гораздо значительнее. Так, напр., Путиловский завод перекатывает болванки сечением в 368 x 368 кв. мм в полосы 191 x 191 кв. мм, а эти последние в тройной длины рельсы площадью поперечного сечения в 41,5 кв. стм, что соответствует утонению слишком в 32 раза. Сила машин при этом применяемых: чернового стана 1500 п. л., отделочного 1800 п. л. Дружковский завод (имеющий рельсопрокатный стан с машиною в 3500 п. л., могущею развивать силу до 5000 п. л.) выкатывает рельсы пятерной, шестерной и даже семерной длины. При поперечных сечениях болванки в 430 x 430 кв. мм и готового рельса в 40 кв. стм утонение производится, следов., в 46 раз. Двигатели прокатных станов для Ф. железа и стали устраиваются разнообразных систем и типов. Простейшие и компактнейшие из них — машины с маховиками, не допускаются перемены направления на ходу и требующие станов с трио-вальцами. И в отношении потребления пара они более экономны, но зато самые станы с трио-вальцами очень сложны; в них трудно добиться точной установки валков (т. е. полного совпадения осей симметрии ручьев); для поднятия металла к верхним валкам требуются специальные механические устройства, и, наконец, от рабочего персонала (вальцовщиков) требуется большое искусство и навык. Поэтому в новейшее время предпочитаются реверсивные машины, дозволяющие работать дуо-вальцами. Как те, так и другие машины устраиваются с переменным расширением пара, чтобы можно было уменьшать впуск пара во время работы в последних ручьях стана, когда не требуется большого расхода движущей силы. Сила прокатных машин в зависимости от избранного распорядка работы изменяется от 500 до 5000 п. л., причем нормальная сила обыкновенно может быть форсируема в значительных пределах. У нас в России сильнейшие рельсопрокатные машины имеются на заводах Дружковском (реверсивная, трехцилиндровая, в 3500 п. л.), Александровском в Екатеринославле (реверсивная двойная, в 3000 п. л.) и Путиловском (двойная реверсивная в 1800 пар. лош. при отделочном стане и таковая же в 1500 пар. лош. при черновом стане); на заграничных заводах встречаются машины силою до 5000 пар. лош. Вышедший из последнего чистового ручья рельс, если оставить его свободно охлаждаться, коробится и искривляется действием неравномерного остывания его тонкой пятки и толстой головки. Поэтому выкатанные рельсы пропускают через правящий прибор, состоящий из нескольких пар вращающихся фигурных роликов; производя давление на рельс, они его правят и вместе с тем продвигают вперед. Выправленный рельс направляется к станку, обрезающему его на должную меру. При этом или сам рельс продвигается после каждого разреза перед круглою пилою, или он остается неподвижным, и разрезка производится одновременно во всех потребных местах несколькими соответственно расставленными пилами. Пилы имеют диаметр в 1—1,5 м и вращаются со скоростью 1500—2000 оборотов в минуту, расходуя каждая до 2 пар. лош. На современных благоустроенных рельсопрокатных заводах все перемещения обрабатываемого металла, как подача болванок из печей к валкам и обратно, передача их от одного ручья к другому и проч., производятся автоматически, при посредстве специально приспособленных механизмов, движимых особыми небольшими паровыми двигателями или электромоторами. Были сделаны попытки выкатки рельсов прямо из жидкой стали, пропуская струю металла в ручей, образованный четырьмя профилированными валками, оси которых образуют четырехугольник и лежат в одной общей горизонтальной плоскости. Металл, вливаемый в этот ручей сверху, быстро остывает, сгущается и выходит из ручья уже в виде Ф. полосы, которая в следующих ручьях подвергается сжатию и уплотнению. Способ этот, однако же, не получил распространения.
Примером прокатки Ф. металла в виде сомкнутых полос может служить прокатка колесных бандажей (фиг. I, №№ 34—39 [К этому же типу кольцевых Ф. металлов относятся угловые кольца, применяемые при постройке паровых котлов и резервуаров.]. Первые бандажи с гребнями приготовлялись из сварочного железа путем сварки концов согнутой железной полосы и оформлением ее в штампах ударами молота. Ненадежность сваренных мест, в которых бандажи часто лопались, заставила прибегнуть к сворачиванию бандажа из более тонкой полосы, которая обвивалась спиралью около оправки и затем проваривалась. Такие бандажи не давали, правда, поперечных трещин, но зато расслаивались по кольцевым сваркам, а потому также были оставлены. Постепенно увеличивавшийся вес подвижного состава и быстрое изнашивание железных бандажей вынудило выделывать их сначала из мелкозернистого сталеватого железа, а затем из пудлинговой стали, при чем не устранялись недостатки железных сваренных бандажей. С изобретением бессемеровского металла все эти способы были постепенно оставлены, так что все бандажи современного подвижного состава выделываются исключительно из литой стали. Слишком жесткий бандаж хрупок и склонен к поломкам, слишком же мягкий скоро изнашивается о жесткие рельсы и невыгоден. На выделку их идет литая сталь с содержанием углерода в 0,34 до 0,40%; марганца от 0,13 до 0,70%; кремния от 0,14 до 0,07% и фосфора от 0,016 до 0,019%. Временное сопротивление ее разрыву от 50 до 70 кгр. на 1 кв. мм; удлинение от 20 до 18%. Болванки отливаются осьмигранного сечения, диаметром в 350, 400, 450 и более мм (смотря по весу бандажа), и имеют высоту, приблизительно равную удвоенному диаметру. Сложность операции превращения массивной болванки в сомкнутое Ф. кольцо заставляет разделять эту работу между молотом и прокатным станом и прибегать к нескольким попутным нагревам, причем каждый нагрев влечет угар в 3%, что необходимо иметь в виду при определении веса сырой болванки. Предположим, что изготовляется паровозный бандаж с внутренним диаметром в 1400 мм профиля h (фиг. I) и весящий в прокатанном виде 382,6 кгр. В течение всей операции потребуется (как пояснено будет ниже) 5 нагревов, поэтому вес болванки должен равняться: 382,6[1 + (5 x 0,03)] = 440 кгр. Этому весу соответствует (при плотности в 7,85) объем в 56000 куб. стм, а этому объему — высота болванки в 600 мм при среднем диаметре в 345 мм. Нагретая до белокалильного жара болванка проковывается (с целью уплотнить металл) под 15-тонным паровым молотом, направляя удары по стрелке P (фиг. XI, А). Проковку прекращают, коль скоро высота болванки уменьшится до 200 мм, а диаметр ее увеличится до 600 мм (фиг. XI, В). Затем под другим (5-тонным) молотом в расплюснутой пластине пробивается штемпелем M (фиг. XII) центральное отверстие диаметр. в 300 м. Для этого пластина укладывается в гнездо наковальни N молота, так что проникание в ее массу штемпеля не вызывает нового увеличения ее диаметра и не вырезает из металла элемента, соответствующего пробитой дыре, а лишь вытесняет металл в окружающую массу и уплотняет его. Это возможно лишь благодаря большой вязкости стали. Пробивка производится в два приема с обоих концов пластины, после чего последняя получает форму, представленную в разрезе на фиг. XIII, А. По окончании этой операции пластина вновь нагревается до белокалильного жара и под третьим (5-тонным) молотом расковывается в кольцо (фиг. XIII, В). Для этого пластина ВВ надевается на цапфу D (фиг. XIV), укрепленную наклонно в наковальне NN, и подвергается частым ударам молота А. После каждого удара кольцо поворачивается на цапфе на небольшой угол. Должная коничность наружного обвода кольца достигается соответственным наклоном цапфы к плоскости бойка молота. Раздав внутреннюю дыру кольца до диаметра в 600 мм, переносят кольцо снова под 15-тонный молот, кладут плашмя и (без нового нагревания) осаживают до толщины 150 мм. После этого кольцо снова нагревается и затем поступает в раскатку на специального устройства прокатных станах. Прокатка заканчивается всего в двух ручьях, черновом и отделочном, так что каждый стан снабжен лишь двумя короткими валками с одним ручьем. Фиг. ХV изображает устройство подобного стана (черный и отделочный станы имеют одинаковое устройство и отличаются лишь размерами ручья). В двух стойках стана помещены пустотелые чугунные валы С и D, несущие на себе взаимно сцепляющиеся шестерни B и А. Верхний вал вращается от машины (120 пар. лош.) и передает вращение нижнему. В гнезда, имеющиеся на передних, свободно выдающихся концах в
Статья про "Фасонные железо и сталь" в словаре Брокгауза и Ефрона была прочитана 1440 раз
|