Трубы металлические
Определение "Трубы металлические" в словаре Брокгауза и Ефрона
Трубы металлические Трубы металлические* Расчет Т. Рассмотрим напряжения, вызываемые в стенках трубы внутреннего радиуса r, толщины стенок δ r, при давлении изнутри p, а извне p + δ p; тангенциальное напряжение материала означим q. Определяя полное давление, действующее на часть стенки Т. единицы длины и соответствующую углу при центре δφ, получаем, что оно равно (p + δ p)(r + δ r) δφ — pr δφ. Этому давлению соответствует напряжение q δ p. δφ. Приравнивая эти выражения и переходя к пределу, имеем p + r[(dp)/(dr)] = q. Напряжения от p и q вызовут в стенке Т. удлинение по оси ее, пропорциональное р + q. Принимая гипотетично, что плоское сечение Т. останется плоским и после деформации, мы видим, что удлинение это не зависит от r, и можем написать p + q = 2A = const. Следовательно: p + r[(dp)/(dr)] = 2А — р; (dp)/(dr) = (2A)/r — (2p)/r. Отсюда p = А + B/r 2, а значит q = А — B/r2. В случае толстостенной Т., подверженной изнутри большому давлению [гидравлический пресс, Т. пушечные], имеем для r = r0, давление (изнутри) р 0, а для r = r1 давление (внешнее) O = p1. Тогда р 0 = А + B/r 02; О = А + B/r 12, так что

— q = ([p0r02]/[(r12 — r02)])(1 + r12/r2) Напряжение от сжатия — q равносильно напряжению от растяжения + f, так что: f = р 0[ r02/(r12 — r02)]x[(r12 + r2)/r2] f maxim, при r = r0 и равно f0 = p0 [(r12 + r02)/(r12 — r02)]. В разных точках стенок Т. f изменяется обратно пропорционально квадрату расстояния от центра. Если при р 0 = 0 материал Т. уже имеет внутренние напряжения, то таковые необходимо алгебраически складывать с вышевыведенными. Пушка делается из нескольких нагоняемых друг на друга под давлением Т.; внутренние Т. сжаты внешними и, наоборот, последние растягиваются изнутри, усилия же при выстреле стремятся растянуть внутренние Т. и т. д.; таким образом, пушка легко выносит большие давления, немыслимые, если бы не было такого предварительного напряжения материала. Для расчета Т., стенки которых, толщиной δ, тонки сравнительно с их диаметром, имеем r0 = R, а r 1 = R + δ; f0 = p0 [(2R2 + 2R δ + δ 2)/(2Rt + t2)] = [(p0R)/ δ ] [1 + δ /R + δ 2/2R2] [1 + δ /(2R)]. При очень малом δ /R, f = (pR)/ δ + p/2, или еще проще: f = p(R1/ δ), если положим R1 = (2R + δ)/2 При расчетах Т. на практике редко пользуются этими формулами для определения толщины стенок, ибо в них не введено ни сопротивление Т. продольному изгибу, ни изнашивание их и т.д., поэтому для каждого рода Т. пользуются особыми простыми проверенными опытами формулами, по большей части чисто эмпирическими. Диаметр Т. в сооружениях рассчитывается так, чтобы сумма процентов и погашения затраченного капитала (увеличивающаяся с диам.) плюс стоимость эксплуатации (уменьшающаяся с увеличением диам.) была minimum. Жаровые Т. паровых котлов, подверженные внешнему давлению, рассчитываются по формуле Баха:

где δ — толщина в см, p давление в кг, l длина жаровой Т. между усиливающими ребрами, d диам. в см, а = 100 для горизонтальных Т. с продольным швом в напуск в один ряд; а = 70 для таких же вертикальных Т.; а = 80 для горизонтальных Т. заварных; а = 50 для таких же вертикальных Т.; с = 0,15, 0,1, 0,01 и 0 при р = 5,67 или более 7 кг. Больших диаметров Т., для провода воды и воздуха (низкого давления), делаются из железных листов, клепаные. Чугунные Т. стали применяться для водоснабжения в начале XVII ст. Версальский водопровод (1678—84) был первой крупной работой этого рода. Городские водопроводы высокого давления начали строиться в половине XIX стол., а с шестидесятых годов появился спрос на Т. для удаления городских нечистот. В настоящее время чугунные Т. составляют предмет массового производства, образующего особую отрасль чугунолитейного дела. Техника ее достигла такой степени развития, что успешно отливаются Т. в 1200 мм диаметром, при толщине стенок всего 20 мм. До 40-х гг. прошлого столетия Т. отливались исключительно в горизонтальном положении, в настоящее время отливка почти всегда ведется в вертикальном положении: при горизонтальном положении формы стержень всплывает, стенки получаются неравномерной толщины, весь находящийся в форме сор и газы, всплывая, сообщают верхней стенке Т. пористость. Следует вести формовку раструбом вниз: это труднее, но зато раструб получается более плотным. Т. малого диаметра (50 — 75 мм) льются раструбом кверху, ибо и так он по принятым для него нормам выходит достаточно прочным. Еще в семидесятых годах прошлого столетия Фруар в Нанси выработал способ отливки, при котором опока при всех работах сохраняет вертикальное положение, не удаляясь со своего места. Способ этот ныне весьма распространен и описан ниже.
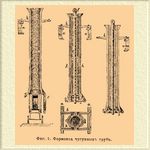 Фиг. 1. Формовка чугунных труб.
На фиг. 1 изображена опока с подвешенной к ней моделью, литейная форма в периоде просушки и готовая для отливки опока со вставленным сердечником. Просушивание производится помощью топки снизу. Сами опоки подвешены на прочных балках аа помощью попере-чин bb, расстояние между которыми изменяется в зависимости от диаметра опок. Последний выбирается так, чтобы между стенкой опоки и моделью оставался зазор, только достаточный для того, чтобы набивка формовочным песком держалась плотно — обыкновенно ок. 25 мм. Сушка такого тонкого слоя продолжается 1 — 2 часа. Модель изготовляется из чугуна и отделывается начисто: посередине ее укреплен железный стержень, служащий для ее опускания и поднимания. Цилиндрическая часть модели по окончании формовки вытягивается кверху, а нижняя часть, отъемная, образующая раструб, вынимается книзу. Нижний затвор опоки образует крышка e, снабженная кольцевой заточкой, служащей для точного установа модели. Эта же заточка служит и для обеспечения правильности положения сердечника, состоящего, аналогично модели, также из двух частей. Изготовление сердечника, набивка опоки и отливка не представляют никаких особенностей. Для высоких давлений Т. производятся по способу Кудлица. Сущность его состоит в том, что опоки не набиваются по модели, а собираются из нескольких отдельных колец, приготовляемых на формовальных машинах и просушиваемых особо. Каждое кольцо имеет с одной стороны выступающий поясок, а с другой впадину. При складывании колец, для большей плотности, стыки смачиваются глиняным раствором. В местах стыков на поверхности Т. замечаются лишь едва заметные наплывы. Отливка Т. ведется из вагранок, а в новейшее время, вследствие падения цен, Т. низкого давления отливают и непосредственно из доменных печей. Фасонные части Т. (колена, крестовины и т. д.) отливаются в горизонтальном положении, в обыкновенных опоках с разрезом по диаметральной плоскости; формовка кривых шишек часто ведется по шаблонам. Очищенные и освобожденные от прибылей Т. испытываются на плотность; водопроводные Т. после закрытия концов крышками наполняются водой под давлением и выстукиваются молотком. При этом Т. не должна пропускать через стенки воду. Газопроводные Т., закрытые с концов, кладутся в воду, и в них нагнетается воздух (до 2 атм.), при этом малейшая неплотность стенок обнаруживается поднимающимися в воде пузырьками. Испытанные Т. взвешиваются. нагреваются до 120° — 150° С и погружаются в асфальтирующий состав:
последний поддерживается в жидком состоянии собственным жаром погружаемых одна за другой Т. Вынутые из состава Т. ставятся наклонно над лотками, по которым излишек состава стекает обратно в резервуар. Те места Т. (внутренность муфт, наружная поверхность конца Т.), с которых слой асфальта должен быть впоследствии удален, перед асфальтированием окрашиваются известковым молоком. Соединение отдельных чугунных Т. между собою производится помощью фланцев или помощью муфт. В первом случае на каждом конце Т. имеется перпендикулярный к оси ее диск. Между обработанными поверхностями двух смежных дисков кладется прокладка из резины, сурикового картона, свинца, кольца красной меди (в заточках) и т. д., и все стягивается болтами. При водопроводах высокого давления в особой заточке зажимают еще резиновое кольцо. Влияние соображений относительно способа изготовления Т., перевозки их, укладки, дополнительных напряжений при перемене темп. и т. д., обусловливающее принятие большей толщины стенок, чем то следовало по расчету, возрастает с уменьшением диаметра Т. Можно принять толщину стенки δ = (D/60) + 7 мм, если рабочее давление не больше 10 атм. Обыкновенно Т. в этом случае и не рассчитываются, а все размеры их (фланцев, болтов и т. д.) по заданному D (диам.) берутся из общепринятых таблиц, напр., германской нормальной таблицы, ибо такие Т. всегда имеются на рынке. Т. для высокого давления рассчитываются, причем к расчетной толщине стенок прибавляется 7 мм в запас на дополнительные напряжения. Число болтов должно быть четное, обыкновенно не меньше 4. Толщина винтов берется не менее 13 мм. В муфтовых Т. конец одной Т. вставляется в раструб соседней Т., а образующейся кольцеобразный шов забивается плетеной просмоленной пенькой, забивается свинцом и подчеканивается. Расчет этих Т. одинаков с расчетом фланцевых. Муфтовые Т. дешевле и поэтому главным образом и применяются для газо- и водопроводов. Фланцевые Т. легче разобрать в случае поломки, а потому они чаще применялись при паропроводах. Из этой сферы их, по мере повышения давления пара, постепенно вытесняют железные варные и цельнотянутые медные Т. Железные варные Т. Для газопроводов не-значительных диаметров (до 90 мм) применяются обыкновенно Т., сваренные в стык. Материалом для них служит пудлинговое, а еще лучше мягкое литое железо, приготовленное на основном поду. Сперва прокатывается плоская полоса ширины, равной будущему диаметру Т., нагревается до светло-красного каления, огибается помощью деревянного молотка около оправки (чугунный параболоид, который на толстом своем конце на длину около 10 — 1 2 мм обточен по внутреннему диаметру Т., насаженный на длинный стержень) и пропускается через волочильное отверстие; для последней операции служат клещи, зажимающие конец полосы и сцепляющиеся с бесконечной движущейся цепью волочильного станка. При этом полоса скатывается в трубку. Затем Т. снова нагревают, пропускают через другое, более узкое, волочильное отверстие или между валками (550—650 мм диам. при 60 — 130 оборотах в минуту) и т. д., пока происходящим сдавливанием шва при проволочке через все уменьшающиеся отверстия не достигнута будет сварка. Затем Т. кладется на чугунную правильную плиту, над которой движется на четырех колесиках взад и вперед другая плита: при этом Т. получает вращательно-поступательное движение и выправляется. В складах имеются обыкновенно такие Т. от 10 до 76 мм диам. Соединяются отдельные Т. помощью муфт, навинчиваемых на нарезанные винтообразно их концы. Т. со швом, сваренным в накладку, обладают гораздо большей прочностью. Они идут как дымогарные, для водотрубных котлов, для паропроводов, нефтепроводов и т. д. У листа железа прежде всего скашивают кромки так, чтобы после свертывания Т. в месте шва не было утолщения. Лист нагревают до светло-красного каления в калильной печи и пропускают через чугунную матрицу особой формы (в начале плоской, потом постепенно переходящей в круглую), причем лист свертывается в Т. Затем эту Т. нагревают до сварочного жара в другой печи и пропускают на оправке через валки особой конструкции: два желобчатых по форме Т. валка-диска вращаются в вертикальной плоскости, а непосредственно за ними два таких же — в горизонтальной; при этом Т. сваривается. Если она не сварится вполне с первого раза, ее снова нагревают, снова пропускают через валки и т. д. Далее Т. правятся, для чего они пропускаются или через волочильное отверстие из белого чугуна, или между двумя наклонно друг к другу поставленными валками формы однополого гиперболоида. Т. получает между ними вращательно-поступательное движение, и получается вполне круглая и правильная. Диаметр таких Т. доходит до 700 мм. Из произведенных в России Т. особого внимания заслуживают Т. керосинопровода из Михайловки до Батума, диам. 200 мм при толщине стенок 8 мм, выдерживавшие пробное гидравлическое давление в 110 атм. Такие Т. соединяются друг с другом помощью муфт и винтовой нарезки, постепенно сходящей на нет; соединение Т. паропроводов производится помощью наваренных заплечиков и свободно надетых на них фланцев, помощью отогнутых краев, зажимаемых между фланцами и помощью напаянных фланцев. Т. водопроводов иногда цинкуют. Наиболее слабое место варной Т. это ее шов; опасность от разрыва Т. по шву уменьшается, если ее сваривать спирально. Для этого сперва сваривается в ленту по длине несколько полос; на особой машине полосы свиваются в спираль, причем Т. постепенно задвигается и поворачивается. Нагревание производится обыкновенно пламенем водяного газа в том только месте, где производится сварка; последняя ведется ударами быстроходного парового молота; этим способом изготовляются Т. лишь большого диаметра (150—625 мм). Соединение таких Т. производится надеванием фланцев с отгибкой бортов, приклепыванием железных или чугунных фланцев и т. д. Волнистые Т. получаются при помощи прокатки в вертикальных станах, подобных бандажным: Т. нагревается в вертикальной цилиндрической печи и переносится на станок, валки которого имеют волнообразную поверхность. На некоторых заводах нет прокатных станов, и волнообразная поверхность получается штамповкой листов под гидравлическим прессом, а затем листы изгибаются и свариваются. Подобные Т. идут на жаровые Т. паровых котлов. Расчитываются они по формуле δ = (pd)/1000 + 0,2 см.
Толщина их не делается меньше 7 мм. Т. для ружейных стволов изготовляются проковкой сплошной болванки и высверливанием ее; иногда они готовятся волочением. Т. для мин, пушечных установок и т. д., сравнительно короткие и толстые, изготовляются ковкой: в болванке помощью пробойника делается выбивка, и образующееся отверстие уширяется путем загонки справки, а затем полученный цилиндр надевается на горизонтально лежащую оправку и при постепенном поворачивании куется под ковочным прессом. Т. без шва по способу Эргардта готовятся из цельной призматической болванки, подобно приготовлению артиллерийских снарядов. Болванку a помещают внутри матрицы b (фиг. 2) и пробивают пунсоном с.
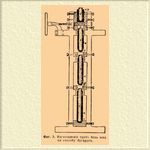 Фиг. 2. Изготовление труб без шва по способу Эргардта.
В это время болванка упирается в задвижку s. Затем последнюю отодвигают помощью винта и прожимают болванку через ряд волочильных отверстий d1, d2. Пунсон движется от штока гидравлического цилиндра. Очень оригинален способ прокатки Т. из цельных болванок Манесмана (способ косой прокатки). Если оси прокатных валков наклонны друг к другу, то поверхности валков производят растяжение болванки, которая, вращаясь, будет одновременно перемещаться поступательно. Если болванка встречает препятствие к своему перемещению, то поступательно перемещаются лишь частицы с поверхности ее, сдвигающие-ся как бы по винтовой линии, и в результате получается Т. Валки делаются коническими или в форме гиперболоида. Если желательно прокатать Т. с очень тонкими стенками, то сперва прокатывают толстостенную Т., а затем на других таких же валках помощью оправки раскатывают ее. Для приведения в движение прокатных станков Маннесмана затрачивается громадная работа (более 2000 HP), причем еще нужно работать с перерывами для накопления запаса работы в маховике. Сама прокатываемая болванка делает до 2800 об. в мин. Работа в этих условиях трудна и дорога. Качество Т. как Эргардта, так и Маннесмана несравненно выше варных. Работа по первому способу гораздо дешевле. Т. велосипедные приготовляются в последнее время из никелевой стали с большим содержанием углерода. Из листа выбиваются круги, кладутся между штампом и матрицей гидравлического пресса и продавливаются. Металл от давления приходит в пластичное состояние и образует чашку с совершенно гладкой поверхностью. Затем чашка переходит с одного пресса на другой и постепенно продавливается все более и более тонкими пунсонами через соответственные матрицы. При прессовке металл закаливается, и его несколько раз отжигают в калильной печи в ретортах (чтобы не образовалось окалины). Для окончательной отделки трубки протягиваются через волочильные станки. Для специальных целей подобным способом готовят и Т. большого диаметра (до 3 00 мм). Медные Т. — Т. из меди, латуни и других сплавов приготовляют, загибая листы этих металлов на деревянной оправке, спаивая шов и протягивая помощью волочильного станка с натяжными клещами несколько раз через волочильную доску. Очень тонкие трубки из золота, серебра и т. д. готовятся следующим образом: тонкие листки разрезаются на полоски, края последних обравниваются и сгибаются в желобок; в последние вставляется тонкая проволока, обмазанная воском, и трубочка плотно огибается вокруг нее. Затем такие трубочки протягивают через волочильную доску, нагревают и вытаскивают из них проволоку. Трубки с открытым швом изготовляются волочением, причем в волочильном отверстия делается язычок, соприкасаясь с которым кромки при проходе трубки через отверстие выправляются.
Фигурные трубочки (ручки для перьев и т. д.) готовят протягиванием грубо приготовленных трубок на деревянном стержне через фигурное отверстие в волочильной доске. Трубки без шва медные и т. д. приготовляются всеми теми же способами, которые применяются для изготовления железных Т. Обыкновенно получают толстостенную Т. и протягивают ее на волочильном станке с натяжными клещами, через постепенно уменьшающиеся глазки. Т. из свинца употребляются для провода жидкостей, когда Т. не подвергаются значительному давлению, и для газопроводов; они легче выдерживают всевозможные из δ гибы, чем Т. железные. Оловянные Т. дороже свинцовых и применяются там, где Т. служат для провода напитков (свинец ядовит). В настоящее время подобные Т. готовят по способу прессования. На фиг. 3 изображен пресс, служащий для этой работы.
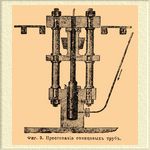 Фиг. 3. Прессование свинцовых труб.
По напорной трубке вода поступает в цилиндр гидравлического пресса со скалкой с, силой до 150000 кг. На штоке скалки насажена другая скалка, со стержнем е, движущаяся в цилиндре g, в который наливается расплавленный металл; при поднятии скалки (немедленно по отвердении металла) металл выжимается в виде кольцевой Т. между стержнем е и стенками отверстия f. Весьма важно, чтобы металл был нагрет почти до температуры плавления, ибо при этом расход на выдавливание наименьший. Для поддержания этой температуры цилиндр g окружен угольной жаровней. Чем меньше диаметр и толщина стенок Т., тем большей длины она за раз получается. Пролуживание или покрывание оловом свинцовых Т. может быть соединено с этим производством, для чего в отверстие Т. при ее выходе наливают расплавленное олово (температура плавления его на 100° меньше, чем свинца), постепенно покрывающее ее стенки по мере выдавливания. Этот слой олова тонок. Гораздо лучше надевать на сердечник е плотно пригнанный оловянный цилиндр, заполнить остальную часть цилиндра g свинцом и продавливать. Т. с рифлями по способу Мюнтца-Лаваля изготовляются из пустотелых болванок раскаткой их между цилиндрическими с ручьями валками и затем расправкой их на валках на оправке. Т. конические без шва готовятся из литых пустотелых болванок (с конической полостью), раскатываемых (фиг. 4) в длинную плоскую полосу. Затем полоса раскатывается на валках (фиг. 5), причем на поверхности ее образуются рифли, сообщающие ей большую сопротивляемость изгибу.
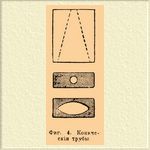 Фиг. 4. Конические трубы.
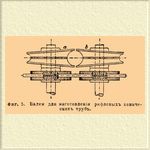 Фиг. 5. Валки для изготовления рифленых конических труб. Такие Т. идут на мачты, столбы и т. д. Гибкие металлические Т. свертываются из прокатанных фигурных полос (фиг. 6), с. прокладкой из асбеста, резины и т. д.
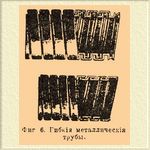 Фиг 6. Гибкие металлические трубы. Для Т. высоких давлений на такую Т. надевается вторая, свитая в противоположном направлении. А. Митинский. Δ.
Статья про "Трубы металлические" в словаре Брокгауза и Ефрона была прочитана 824 раз
|